tapeout(Tapeout A Crucial Step in Integrated Circuit Manufacturing)
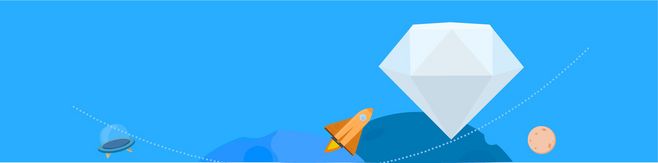
Tapeout: A Crucial Step in Integrated Circuit Manufacturing
Introduction
Integrated circuits (ICs) are a fundamental component of modern electronic devices. These miniature electronic circuits contain hundreds of thousands, if not millions, of transistors and other electronic components. The manufacturing process for ICs involves multiple intricate steps, with tapeout being a critical milestone. In this article, we will explore the significance of tapeout in the IC manufacturing process.
What is Tapeout?
Tapeout refers to the final stage of the IC design phase before fabrication begins. Once the design team has completed the layout and verification of the IC, the circuit's blueprint is transferred to a mask set. The mask set consists of multiple photomasks, which act as stencils for the various circuit layers' patterns. Tapeout involves the preparation and delivery of the mask set to the semiconductor foundry or fabrication facility.
Importance of Tapeout
Tapeout marks a significant milestone in the IC manufacturing process. It signifies the completion of the design phase and the readiness to move forward with the fabrication process. The successful tapeout of an IC design is vital for meeting project timelines, as any delays or issues in this stage can potentially impact the overall production schedule.
Key Steps in Tapeout
1. Verification and Validation: Before initiating the tapeout process, it is crucial to ensure the design is thoroughly verified and validated. This step involves several checks, including design rule checks (DRC) and layout versus schematic checks (LVS), to ensure that the design adheres to the manufacturing rules and specifications.
2. Mask Preparation: Once the design has passed the verification and validation phase, the mask set preparation begins. This step involves generating the photomasks that will be used in the fabrication process. The masks are created using highly precise lithographic techniques, with each mask representing a different layer of the IC design.
3. Tapeout Delivery: After the mask preparation is complete, the mask set is packaged and sent to the semiconductor foundry or fabrication facility. The foundry will then use the masks to transfer the circuit patterns onto the silicon wafers using various processes such as etching, deposition, and doping.
Challenges in Tapeout
1. Design Complexity: As IC designs continue to evolve and become more complex, tapeout poses several challenges. The increased transistor density and shrinking feature sizes require greater precision in mask creation and fabrication processes.
2. Time Constraints: In today's competitive market, time-to-market is a critical factor. Tapeout delays can have severe implications, ranging from missed product launch dates to financial losses. Thus, efficient project management and coordination among design, validation, and fabrication teams are essential to meet tight tapeout deadlines.
Conclusion
Tapeout serves as a crucial step in the IC manufacturing process, bridging the gap between design and fabrication. It represents the completion of the design phase and signals the readiness to proceed with fabrication. The success of tapeout ensures that the IC project remains on track and meets the required project timelines. With the increasing complexity of IC designs, efficient management and coordination among various teams become vital for a smooth and timely tapeout process.